does anyone know if this plinth is real obsidian?
All of them are composite. The B5/7 were the last evolution and are TNRC.
@warrjon
Although you are right re bearing fragility with that range of arms I was actually referring to the Obsidian plinths when mentioning fragility.
You really do need to treat those plinths with the greatest care. I would now hesitate to use one without ensuring that
nothing could possibly drop on it and also would use a torque wrench at a low setting when connecting the unit to the plinth.
I had the best results from really solid arms especially the Fidelity Research 64S and Wheaton Triplanar...even the old Zeta
worked better for me than any of those beautifully made Technics arms....but that was due to my choice of MC cartridges.
Although you are right re bearing fragility with that range of arms I was actually referring to the Obsidian plinths when mentioning fragility.
You really do need to treat those plinths with the greatest care. I would now hesitate to use one without ensuring that
nothing could possibly drop on it and also would use a torque wrench at a low setting when connecting the unit to the plinth.
I had the best results from really solid arms especially the Fidelity Research 64S and Wheaton Triplanar...even the old Zeta
worked better for me than any of those beautifully made Technics arms....but that was due to my choice of MC cartridges.
SH-10B7 obsidian plinth question:
Looking at this ad for an SP-10R with EPA-100mk2 and SH-10B7 plinth.
https://j-corder.com/shop/ols/products/technics-sp-10r-wobsidian-plinth--epa-100-mk2-boron-tonearm
Seems like a reasonable deal for the new (albeit unboxed) SP-10R and the EPA-100mk2 (claimed to be in perfect condition) alone, but my wife is taken with the obsidian plinth. Dragon glass! I think she's preparing for the White Walkers. I think this plinth is actually an SH-10B5, though the add says SH-10B7, and my question is: does anyone know if this plinth is real obsidian? I've searched and searched and mostly found contradictory information.
Sh10B5 or Sh10B7? You should ask the seller; behind the base there is a badge just read what it is,
alternatively the B5 base has the circular hole to house the motor the B7 base has the square hole.
It involves obsidian powder and binders all poured into a mold to obtain the desired shape and obtain constant production, the lead screws are applied and cemented to the lower side, finally the upper surface is vitrified with a process unknown to me... this is not applied paint.
I have auditioned an SL1000mk2 many years ago and was not impressed. The tonearm and cartridge may have been responsible for my luke-warm reception, but subsequent experiments have persuaded me that the OEM plinths, despite the Technics hype, are greatly over-rated.I had an SL1000mk2 herewith the Obsidian plinth and IMO is not worth it. You would be far better off with a Permalli/Panzerholtz plinth. At $13,000 I think you can do much better with an SP10mk2 and a Panzer plinth and SME-IV which will most likely cost you around 1/2 of that.
@Bon has both SP10R and mk2 if he sees this he can give you his opinion.
I have used the mk2 in a number of custom diy plinths since 1998 and it has evolved to become my daily turntable of choice. It has a modified kaneta style plinth of resin-bentonite, and the build is described elsewhere in this thread. Warrjon has further modified the mk2 by moving to Panzerholz/Permali, but I have not auditioned the combination.
Since 2018, I have owned a 10R, installed in various resin/bentonite plinths. The modified mk2 and 10R in the resin/bentonite plinths are excellent performing turntables, but in my system to my ears, I prefer the mk2. Both turntables have SME IV tonearms installed.
Attachments
Thank you all very much, and I think I've got my definitive answer on those Technics plinths: not obsidian. (My wife will be so disappointed.) Me, I love those gorgeous dense wood plinths that you all have been making, but whereas I've got some DIY electronics chops, I've got bupkis when it comes to woodworking.
The company where I get my Permalli has a CNC router. One SP10mk2 owner had his Permalli plinth CNC cut which is what prompted me to try Permalli, here is a pic of his TT. The aluminium is necessary to prevent the Permalli from warping even though the Permalli is 2x30mm panels it can still warp.
Once everything is cut it's pretty easy to glue up with epoxy.
Another option if you are up for it is to remove the motor from the chassis and install it in a separate plinth. Here is an SP10mk2 I did for a friend. The motor is bolted directly to the Permalli with an umbilical cord to the electronics still housed in the OEM chassis. I built the Permalli plinth from offcuts, The cutout for the motor was made with a regular router and a circle jig. The angles were cut on my milling machine.
There is a guy over on Lenco Heaven that can CNC plinths for a reasonable price out of India. He posted in this thread a little while ago.
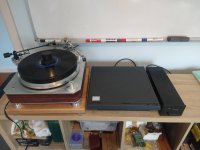
Once everything is cut it's pretty easy to glue up with epoxy.
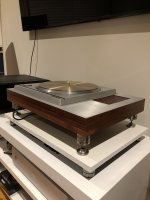
Another option if you are up for it is to remove the motor from the chassis and install it in a separate plinth. Here is an SP10mk2 I did for a friend. The motor is bolted directly to the Permalli with an umbilical cord to the electronics still housed in the OEM chassis. I built the Permalli plinth from offcuts, The cutout for the motor was made with a regular router and a circle jig. The angles were cut on my milling machine.
There is a guy over on Lenco Heaven that can CNC plinths for a reasonable price out of India. He posted in this thread a little while ago.
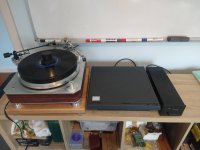
@rdb64 I am also very familiar with the Mk II used in Plywoods ranging from:
600Kg/m3 (Birch Marine Plywood ) -
850Kg/m3 (MU25 - Densified / Non Resin Impregnated ) -
1400Kg/m3 (Phenolic Resin Impregnated Densified Wood) of which Panzerholz or Permali are Brands for this material type.
Phenolic Resin Impregnated Densified Wood is the one to go for, it is also usually Delignified, creating a highly compressible wood fibre.
I have been demo'd all Three of the above Plinth Materials, on the same Mounting Set Up, withe the same design removable Headshell Tonearm and Cartridge.
The Phenolic Resin Impregnated Densified Wood is the material that has made the best impression.
As a basic description, it is hard to believe the end sound being produced can be tidied up any better once having heard the improvement it creates.
To have more option on Colour with a Phenolic Resin Impregnated Densified Wood, there is a Dymond Wood that is a suitable substitute for P'holz or P'mali.
The Link will show you the supplier.
https://webbwood.com/
To select your Wood make sure you have decided how many Tonearms are wanted to be mounted? the Board Size will be larger for increased Tonearm Mounting.
Usually, a Resin Impregnated Board Selected is 25mm ( 1 Inch ) Thick, with 25 Plies as the minimum to produce the end thickness.
More Plies to produce the end thickness is an attractive option such as Picawood, maybe Webb have such an option on offer.
Cross Grain Plies is very important, not only for Strength, but also for the additional dissipation that is created, a third grain orientation would be even more interesting, but the only place I have surmised that has this, is Kaiser Speakers as a special order material they call Tankwood.
600Kg/m3 (Birch Marine Plywood ) -
850Kg/m3 (MU25 - Densified / Non Resin Impregnated ) -
1400Kg/m3 (Phenolic Resin Impregnated Densified Wood) of which Panzerholz or Permali are Brands for this material type.
Phenolic Resin Impregnated Densified Wood is the one to go for, it is also usually Delignified, creating a highly compressible wood fibre.
I have been demo'd all Three of the above Plinth Materials, on the same Mounting Set Up, withe the same design removable Headshell Tonearm and Cartridge.
The Phenolic Resin Impregnated Densified Wood is the material that has made the best impression.
As a basic description, it is hard to believe the end sound being produced can be tidied up any better once having heard the improvement it creates.
To have more option on Colour with a Phenolic Resin Impregnated Densified Wood, there is a Dymond Wood that is a suitable substitute for P'holz or P'mali.
The Link will show you the supplier.
https://webbwood.com/
To select your Wood make sure you have decided how many Tonearms are wanted to be mounted? the Board Size will be larger for increased Tonearm Mounting.
Usually, a Resin Impregnated Board Selected is 25mm ( 1 Inch ) Thick, with 25 Plies as the minimum to produce the end thickness.
More Plies to produce the end thickness is an attractive option such as Picawood, maybe Webb have such an option on offer.
Cross Grain Plies is very important, not only for Strength, but also for the additional dissipation that is created, a third grain orientation would be even more interesting, but the only place I have surmised that has this, is Kaiser Speakers as a special order material they call Tankwood.
Thank you, @warrjon and @JohnnoG. Those densified wood plinths are clearly the way to go, and the ones you all have built look fab (even if they don't provide any protection from White Walkers). Since I have no such woodworking chops, next step is to find someone who can do it on commission. From this thread and online search, I know of Artisan Fidelity, and we have a friend who is an excellent furniture maker and luthier (though I don't think he's ever done a turntable). Those are the only options I know of.
With a Densified Wood at approx' 1400Kg/m3.
This is able to be machined very similar to a metal, which also leaves a local machine ship as an option as well.
The wood is able to be Milled to Rebate or CNC Rebated, for the ultimate accuracy.
Attempt to keep the fastening centres to a very very tight tolerance, and the Platter Spindle > Pivot Centre on the Tonearm dimension is also best if kept to the tightest of tolerance. These tightness of a dimension is a desirable end result if rigid coupling and maintained geometry is the goal.
The Link is a Template for a SP10 MK ? hopefully a member can confirm if it suits the MkII.
A Template will enable the Plinth to be produced by a wider option of services.
The wonderment of the forum, is being introduced to individuals with very good skill sets, who may not be too far from the home.
I suggest the Off Cuts are retained as well, with one purpose for them, to be used to produce a set of Conical Footers that are Height Adjustable. Three or Four Footer is another debateable support method.
A Densified Wood used as a Sub Plinth has produced exceptional results when used in conjunction with a D'fied Wood Plinth and other Plinth Materials.
My usage of the D'wood Sub Plinths, has shown the Value of it in use, supporting a Valve Phonostage, and this positive outcome extends to Valve Amplification owned by others and my own and other owned CD Source.
I surmise a Value will be found with SS Devices as well.
I don't see how a Professionally produced design aimed at the Commercial Market, that has started to adopt these wood types as the structure, is going to outperform a very well executed non Commercial production.
If it helps reinforce your intention both Clearaudio and Linn are now using this wood type in their TT's where Prices range between $20K - $60K.
Imagine how a Company producing Plinths only, can play with such an information to make their own offering to the Market seem extremely attractive.
https://www.fromjapan.co.jp/japan/en/auction/yahoo/input/j1132884498/
This is able to be machined very similar to a metal, which also leaves a local machine ship as an option as well.
The wood is able to be Milled to Rebate or CNC Rebated, for the ultimate accuracy.
Attempt to keep the fastening centres to a very very tight tolerance, and the Platter Spindle > Pivot Centre on the Tonearm dimension is also best if kept to the tightest of tolerance. These tightness of a dimension is a desirable end result if rigid coupling and maintained geometry is the goal.
The Link is a Template for a SP10 MK ? hopefully a member can confirm if it suits the MkII.
A Template will enable the Plinth to be produced by a wider option of services.
The wonderment of the forum, is being introduced to individuals with very good skill sets, who may not be too far from the home.
I suggest the Off Cuts are retained as well, with one purpose for them, to be used to produce a set of Conical Footers that are Height Adjustable. Three or Four Footer is another debateable support method.
A Densified Wood used as a Sub Plinth has produced exceptional results when used in conjunction with a D'fied Wood Plinth and other Plinth Materials.
My usage of the D'wood Sub Plinths, has shown the Value of it in use, supporting a Valve Phonostage, and this positive outcome extends to Valve Amplification owned by others and my own and other owned CD Source.
I surmise a Value will be found with SS Devices as well.
I don't see how a Professionally produced design aimed at the Commercial Market, that has started to adopt these wood types as the structure, is going to outperform a very well executed non Commercial production.
If it helps reinforce your intention both Clearaudio and Linn are now using this wood type in their TT's where Prices range between $20K - $60K.
Imagine how a Company producing Plinths only, can play with such an information to make their own offering to the Market seem extremely attractive.
https://www.fromjapan.co.jp/japan/en/auction/yahoo/input/j1132884498/
@rdb64
Acoustand makes a large range of SP-10 plinths -
https://www.acoustand.co.uk/collections/acoustand-technics-sp10-series-plinths
Acoustand makes a large range of SP-10 plinths -
https://www.acoustand.co.uk/collections/acoustand-technics-sp10-series-plinths
Thank you, @warrjon and @JohnnoG. Those densified wood plinths are clearly the way to go, and the ones you all have built look fab (even if they don't provide any protection from White Walkers). Since I have no such woodworking chops, next step is to find someone who can do it on commission. From this thread and online search, I know of Artisan Fidelity, and we have a friend who is an excellent furniture maker and luthier (though I don't think he's ever done a turntable). Those are the only options I know of.
A good many people find no issue with the Technics plinths. Quite a premium on the B7 being the rarest one.
...
If it helps reinforce your intention both Clearaudio and Linn are now using this wood type in their TT's where Prices range between $20K - $60K.
...
https://www.fromjapan.co.jp/japan/en/auction/yahoo/input/j1132884498/
Huh? The whole point of the Linn Keel is to remove the plinth from the equation. Sure, you still have the Trampolin andyes the plinth does some work, other that being nice looking... but the whole point of the Keel is to mechanically link the tonearm with the turntable.
When I look at the Technics design, I'm surprised that the table and tonearm are kept separate. Has no one attempted to do a Keel like linkage between table and tonearm? Is it because of motor vibrations? ( a belt drive removes those vibrations ).
Jim, I'm serious, not needling you.
@tonyEE Once the SP10 chassis is bolted to the plinth it becomes a very rigid coupling. Even better if the motor is removed from the SP10 chassis and installed separately in a good plinth. Artisan Fidelity and Steve Dobbins have been do this to the SP10 mk2 and mk3 for years.
I owned an LP12 for 30years and when I bought the SP10mk2 it was a much better sounding TT than the LP12. The Keel is a good upgrade over the old resonant subchassis. Linn have made a plinth from Panzerholtz. Keep in mind even a spring suspended TT will transmit vibration through the springs above their resonant frequency. Those springs will transmit 1kHz with ease. The Pz plinth will go a long way to lowering the amount of energy in the plinth that will be transmitted to the subchassis and thus to the arm/cartridge.
@rdb64 The Technics plinth is definitely not bad and probably anywhere as good as a plywood plinth. I've had an SP10mk2 in an SH-10B7 plinth and I also heard the mk2 in the Permalli plinth I posted above. It was this Permalli plinthed mk2 that was the catalyst for me to build my Permalli plinth it was that much better.
@analogadikt is the person the contact who can CNC Permalli out of India. Hopefully he'll see this and chime in
I owned an LP12 for 30years and when I bought the SP10mk2 it was a much better sounding TT than the LP12. The Keel is a good upgrade over the old resonant subchassis. Linn have made a plinth from Panzerholtz. Keep in mind even a spring suspended TT will transmit vibration through the springs above their resonant frequency. Those springs will transmit 1kHz with ease. The Pz plinth will go a long way to lowering the amount of energy in the plinth that will be transmitted to the subchassis and thus to the arm/cartridge.
@rdb64 The Technics plinth is definitely not bad and probably anywhere as good as a plywood plinth. I've had an SP10mk2 in an SH-10B7 plinth and I also heard the mk2 in the Permalli plinth I posted above. It was this Permalli plinthed mk2 that was the catalyst for me to build my Permalli plinth it was that much better.
@analogadikt is the person the contact who can CNC Permalli out of India. Hopefully he'll see this and chime in
@tonyEE There is no need for a “keel” type of thing on these tables. This is an SP-10 thread, not an LP-12 thread. The keel is trying to fix an issue that rigid tables don't have.
Suspended subchassis vs rigid turntables are two different ways to solve the same issue, but there is still some apples to oranges in the comparison. But the arm is attached to the same vibrational plane as the motor and the platter… I.E., it’s all rigidly bolted together. A suspended table usually has the arm and platter together, which is good as it’s wobbling around together and will stay in alignment to each other, but the vibration from the LP-12 motor will still be transmitted through the belt, although the belt does act as a fairly good low-pass filter for said vibrations. It’s significantly better (and significantly more difficult) to make a motor that has no vibrations.
Anyway, enough about LP-12 and other off-topic turntables.
Suspended subchassis vs rigid turntables are two different ways to solve the same issue, but there is still some apples to oranges in the comparison. But the arm is attached to the same vibrational plane as the motor and the platter… I.E., it’s all rigidly bolted together. A suspended table usually has the arm and platter together, which is good as it’s wobbling around together and will stay in alignment to each other, but the vibration from the LP-12 motor will still be transmitted through the belt, although the belt does act as a fairly good low-pass filter for said vibrations. It’s significantly better (and significantly more difficult) to make a motor that has no vibrations.
Anyway, enough about LP-12 and other off-topic turntables.
Ay... does the SP-10 benefit from a specific type of base?
Certain non SP tables require specific types of bases.... like the Target TT5T that I use. Sometimes the base is as important as the table proper.
Besides, he ( @JohnnoG ) brought up the Linn and Clearaudio tables ).... not me... hmm.... I'm just amazed at how much attention is given in the SP world to the plinth.
Certain non SP tables require specific types of bases.... like the Target TT5T that I use. Sometimes the base is as important as the table proper.
Besides, he ( @JohnnoG ) brought up the Linn and Clearaudio tables ).... not me... hmm.... I'm just amazed at how much attention is given in the SP world to the plinth.
I think the attention given the plinth is because most people do their own thing in that regard. Sure, there’s a decent number of Technics plinths out there and being used, but I suspect it’s not even close to the majority. Most people have one made or make their own. It’s a chance to do something interesting or pretty or both.
@tonyEE the plinth is important it does more than just attach the arm to the motor. It also has to deal with the energy created by the stylus tracking the groove as well as seismic and airborne vibration.
Most underestimate the amount of energy that the platter/plinth need to deal with. If this energy is not attenuated it will reflect back to the stylus and will mix with the signal and smear the music. In a revealing system the difference in sonic performance of an SP10 in a plywood plinth and a Resin/Bentonite or Permalli plinth is clearly audible. The better plinth attenuates this energy and more detail is audible.
My SP10 sits on a sand box on a Minus K. The Minus K deals with the low frequency vibration it's seismic isolation is extremely good but it allows higher frequency like 1kHz through which is not an issue as seismic is very low frequency. The sand box loads the Minus K to close to its limit and also becomes a sink for energy generated by the TT.
Most underestimate the amount of energy that the platter/plinth need to deal with. If this energy is not attenuated it will reflect back to the stylus and will mix with the signal and smear the music. In a revealing system the difference in sonic performance of an SP10 in a plywood plinth and a Resin/Bentonite or Permalli plinth is clearly audible. The better plinth attenuates this energy and more detail is audible.
My SP10 sits on a sand box on a Minus K. The Minus K deals with the low frequency vibration it's seismic isolation is extremely good but it allows higher frequency like 1kHz through which is not an issue as seismic is very low frequency. The sand box loads the Minus K to close to its limit and also becomes a sink for energy generated by the TT.
We agree on the coupling of the tonearm to plinth to table. Some tables do it directly, bypassing the plinth. Not only the Linn, but also the Rega Planar 8 and 10. Where the goal is to minimize the impact of the plinth on the vibrations.
At the risk of Jim yelling at me again...
I'd guess the base of the table (not the plinth) then depends on the design of the table? Whether sprung or not.
An old acquaintance of mine used to have his vacuum Sota on 500 lbs of concrete blocks in his garage... with phono preamp... 20 feet from the line stage. I used to joke he never heard the lead in groove.
In the Linn, a heavy base robs the sound. The Target TT5 is perfect, I've tried heavy stands and they just don't work. They deaden the sound... kills off the pace of the music. (yeah, I know, same old words, but that's what it does).
I'd suppose the SP tables are on the Sota side of the house, they prefer a very heavy base to transfer the vibrations away? Is the plinth of an SP then single sprung? The components tightly couples to the plinth and then the latter is sprung? As opposed to the Linn which is doubly sprung with the internal spring and then the Trampolin feet.
To each his own, I guess.... whether to tango or disco.
At the risk of Jim yelling at me again...
I'd guess the base of the table (not the plinth) then depends on the design of the table? Whether sprung or not.
An old acquaintance of mine used to have his vacuum Sota on 500 lbs of concrete blocks in his garage... with phono preamp... 20 feet from the line stage. I used to joke he never heard the lead in groove.
In the Linn, a heavy base robs the sound. The Target TT5 is perfect, I've tried heavy stands and they just don't work. They deaden the sound... kills off the pace of the music. (yeah, I know, same old words, but that's what it does).
I'd suppose the SP tables are on the Sota side of the house, they prefer a very heavy base to transfer the vibrations away? Is the plinth of an SP then single sprung? The components tightly couples to the plinth and then the latter is sprung? As opposed to the Linn which is doubly sprung with the internal spring and then the Trampolin feet.
To each his own, I guess.... whether to tango or disco.
Last edited:
- Home
- Source & Line
- Analogue Source
- The Incredible Technics SP-10 Thread